
Co
Cobalt
Umicore’s cobalt powders have not only a high elastic limit but also moderate abrasive grain holding power because of its low plasticity. Its biggest advantage is suppression of carbonization of diamond grits during sintering, which is difficult to prevent with standard cobalt powder. To meet the wide-ranging needs of customers, there is a wide assortment of products, including pure cobalt, cobalt premixed with WC, granulated powder, low cobalt powder “Cobalite,” and cobalt for cemented carbide.
Manufacturer introduction
Based in Brussels, Belgium, Umicore (formerly Eurotungstene) is a global manufacturer in the production, conversion, and recycling recovery of catalysts and nonferrous metals. The organization of several mining and smelting companies, now known as Umicore, has a history of more than 200 years since its predecessor was founded in 1805.
Umicore offers a wide variety of cobalt and alloy powders, primarily for diamond tools and superalloys, for use in stone cutters, construction, metal cutting tools, and consumable parts. Product applications are diverse and include one of the essential raw materials for the growing secondary battery industry, rubber tire manufacturing, pigments for the ceramic industry, catalysts for paint drying and resin production, and surface treatments.
Main characteristics of cobalt
- It has excellent stability on both grain size and hardness over a wide range of sintering temperatures, and guarantees homogeneity in segment production.
- Quality assurance: A sintering test is conducted for each lot at the company’s laboratory.
- It is characterized by very low reactivity to diamond.
- Improvement of the mechanical properties of the sintered segment: While the elastic limit is high, it has moderate holding power during cutting because of its low plasticity.
Pure Cobalt Grades (Formerly products of EuroTungsten)
5 grades of Cobalt powders, specially designed for the Diamond Tool industry.
・Grain size from 0.90 to 3.50 μm
・Hardness from 103 HRB to 110 HRB (hot pressing)
Grade | Fisher grain size (μm) | Scott density (g/c㎡) | Minimum sintering temperature | Recommended sintering temperature |
CO7106(COUF) | 0.9 | 0.8 | 775℃ | 800℃ |
CO6105(COF) | 1.25 | 0.9 | 800℃ | 825℃ |
CO6101(COC) | 1.6 | 0.9 | 825℃ | 850℃ |
CO6102(COD) | 1.8 | 1.0 | 825℃ | 850℃ |
CO6106(COH) | 3.5 | 1.45 | 825℃ | 925℃ |
Pure Cobalt Grades (Umicore products)
In addition to the old Eurotungsten products, we also sell the following Umicore Cobalt products.
Grade | Fisher grain size (μm) | Scott density (g/c㎡) | Tap density (g/c㎡) | Grain size distribution | ||
D10 Laser diffraction, dry (μm) | D50 Laser diffraction, dry (μm) | D90 Laser diffraction, dry (μm) | ||||
Cobalt 400 Mesh | 3.8 | 1.9 | 3.0 | 4.5 | 10.5 | 18.0 |
Cobalt Extra Fine | 1.45 | 1.2 | 2.5 | 1.4 | 3.6 | 8.5 |
Cobalt Half Micron | 0.7 | 1.2 | 2.3 | 1.4 | 2.6 | 4.9 |
Cobalt Ultrafine | 0.9 | 1.2 | 2.5 | 1.7 | 3.2 | 6.0 |
Cobalt premix Grades
Grade | Tungsten carbide (%) | Cobalt (%) | Scott density (g/c㎡) | Theoretical density (g/c㎡) | Recommended sintering temperature | Vickers hardness | Brinell hardness |
ME1108 | 10 | 90 | 0.9 | 9.3 | 850℃ | 350 | 340 |
Cobalt granules
2 grades of pure Cobalt powders (CO7106、CO6102) and 1 grade of WC-Co premixed powders (ME1107) are available as granules of 63 to 450 μm, or 250 to 630 μm.
The main advantages of granules are :
・Good flow ability
・Limited of dust generation during handling and processing
・Higher apparent density
Base | Granules | Scott density (g/c㎡) | Tap density (g/c㎡) | Hall flow (s/50g) | Binder (%) | Granule size (μm) |
CO7106 | CO5106 | 2.3 | 2.6 | 8.0 | 2.75 | 63 – 450 |
CO6102 | CO5102 | 2.0 | 2.3 | 9.0 | 2.5 | 63 – 450 |
CO5112 | 2.0 | 2.3 | 9.0 | 3.0 | 250 – 630 | |
ME1107 | ME5107 | 2.6 | 2.9 | 7.0 | 2.75 | 63 – 450 |
ME5117 | 2.7 | 3.0 | 7.0 | 2.75 | 250 – 630 |
Cobalite®
Cobalite® is a practical product, less influential on a human body because of minor cobalt content.
Grade | Fisher grain size (μm) | Cobalt (%) | Cu (%) | Fe (%) | Real density (g/c㎡) | Tap density (g/c㎡) | Grain size distribution d50 (μm) | Recommended sintering temperature |
Cobalite CNF※ | 2.2 | – | 26 | 68.4 | 8.18 | 1.5 – 2.3 | 12 | 800 – 850℃ |
Cobalite 601 | 5.5 | 10 | 20 | 70 | 8.16 | 2.2 – 3.0 | 10 | 775℃ |
Grade | Fisher grain size (μm) | Theoretical density (g/c㎡) | Scott density (g/c㎡) | Tap density (g/c㎡) | Oxygen (%) | Minimum sintering temperature | Recommended sintering temperature |
Cobalite UMHDR | 5.5 | 8.19 | 2.4 | 3.5 | 0.4 | 750℃ | 850℃ |
Cobalt for hard metal
Both spherical and elongated cobalt powders suitable for various applications are available. Cemented carbide tools are widely used for the automobile industry as cutting tool inserts, drills for petroleum and natural gas exploration, electronic equipment (PCB drill), metal molds (molding, punching), etc.
Grade | Fisher grain size (μm) | Cobalt (%) | Oxygen (%) | Ca (%) | Fe (%) | Ni (%) | Si (%) |
CO6104 | 1.25 | 99.9 | 0.5 | 0.002 | 0.003 | 0.03 | 0.002 |
CO6124 | 1.25 | 99.9 | 0.5 | 0.002 | 0.003 | 0.06 | 0.002 |
CO6004 | 0.9 | 99.9 | 0.5 | 0.002 | 0.003 | 0.06 | 0.002 |
Grade | Fisher grain size (μm) | Scott density (g/c㎡) | Tap density (g/c㎡) | Grain size distribution | ||
D10 Laser diffraction, dry (μm) | D50 Laser diffraction, dry (μm) | D90 Laser diffraction, dry (μm) | ||||
Half Micron Powder | 0.65 | 1.2 | 2.4 | 1.2 | 2.5 | 4.7 |
Ultrafine Powder | 0.90 | 1.2 | 2.5 | 1.7 | 3.3 | 5.8 |
Spherical Extrafine Powder | 1.2 | 1.3 | 2.7 | 2 | 4 | 8 |
Cobalt 100 Mesh | 3.8 | 1.8 | 2.9 | 5 | 12 | 20 |
Packing
We supply products on a metal drum with a polyethylene inner bag. For drum sizes, please contact us.
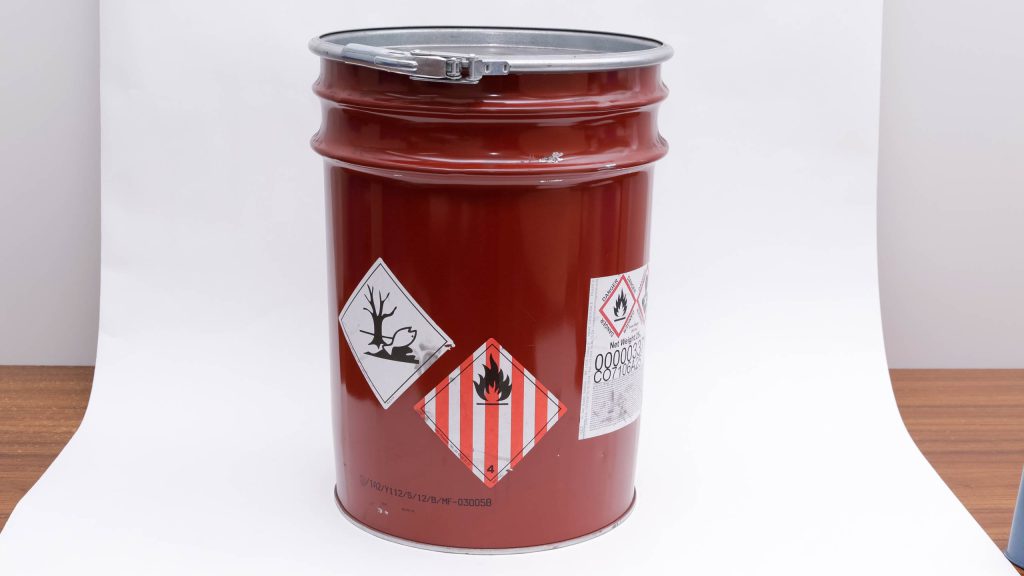
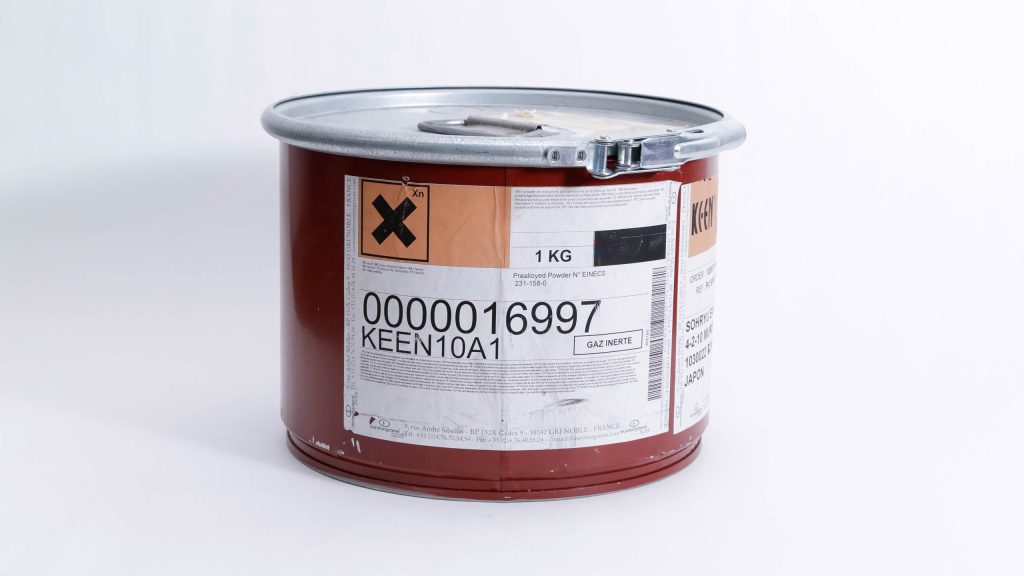