
NEXT®
Alloyed powder
NEXT® is widely used as a standard metal alloy powder in the diamond tool industry. NEXT® is a cobalt-iron-copper alloy powder and can be mixed with various types of metal powders for use. NEXT® contributes to cost reduction and offers a more stable price than conventional metal powders.
Compared to standard premixed powders, NEXT® is composed of finer grains, has higher homogeneity, and offers superior metal dispersion. It has excellent diamond retention and improves tool life and performance.
Manufacturer introduction
Based in Brussels, Belgium, Umicore (formerly Eurotungstene) is a global manufacturer in the production, conversion, and recycling recovery of catalysts and nonferrous metals. The organization of several mining and smelting companies, now known as Umicore, has a history of more than 200 years since its predecessor was founded in 1805.
Umicore offers a wide variety of cobalt and alloy powders, primarily for diamond tools and superalloys, for use in stone cutters, construction, metal cutting tools, and consumable parts. Product applications are diverse and include one of the essential raw materials for the growing secondary battery industry, rubber tire manufacturing, pigments for the ceramic industry, catalysts for paint drying and resin production, and surface treatments.
NEXT® Grades
Grade | Fisher grain size (μm) | Theoretical density (g/c㎡) | Scott density (g/c㎡) | Tap density (g/c㎡) | Minimum sintering temperature | Recommended sintering temperature |
NEXT®100 | 1.15 | 8.62 | 0.8 | 1.95 | 825℃ | 850℃ |
NEXT®200 | 1.15 | 8.75 | 0.75 | 1.75 | 700℃ | 725℃ |
NEXT®300 | 4.2 | 8.12 | 2.2 | 3.2 | 775℃ | 825℃ |
NEXT®400 | 3.0 | 8.08 | 1.6 | 2.6 | 825℃ | 850℃ |
Pre-alloyed powders are composed of 3 metals : Cobalt, Iron and Copper.
The range consists in 4 grades of pure NEXT® whose properties can be optimized by mixing with traditional additives.
NEXT® Premixed Grades
Grade | Theoretical density (g/c㎡) | Scott density (g/c㎡) | Tap density (g/c㎡) | Minimum sintering temperature | Recommended sintering temperature |
MX1180 | 9.49 | 1.0 | 2.2 | 825℃ | 850℃ |
MX1480 | 8.47 | 1.0 | 2.0 | 750℃ | 800℃ |
MX2480 | 8.58 | 1.0 | 2.1 | 700℃ | 750℃ |
MX3480 | 8.07 | 2.3 | 3.4 | 750℃ | 825℃ |
MX1660 | 9.29 | 1.2 | 2.5 | 800℃ | 850℃ |
MX1760 | 8.51 | 1.1 | 2.4 | 725℃ | 775℃ |
NEXT® Granules Grades
Grade | Granule size (μm) | Scott density (g/c㎡) | Tap density (g/c㎡) | Hall flow (s/50g) | Binder (%) |
NEXT®101 | 63 – 450 | 2.3 | 2.6 | 8.0 | 2.75 |
NEXT®201 | 63 – 450 | 2.3 | 2.7 | 8.0 | 2.75 |
MX1481 | 63 – 450 | 2.3 | 2.6 | 7.0 | 2.75 |
MX3481 | 63 – 450 | 2.5 | 2.8 | 6.5 | 2.75 |
NEXT® Free sintering solution Grades
Grades | Fisher grain size (μm) | Theoretical density (g/c㎡) | Scott density (g/c㎡) | Tap density (g/c㎡) | Minimum sintering temperature | Recommended sintering temperature | |
Powders | NEXT®400 | 2.0 | 1.2 | 2.4 | 8.35 | 875℃ | 900℃ |
MX4885 | – | 1.1 | 2.2 | 8.21 | 900℃ | 950℃ | |
MX4380 | – | 1.0 | 2.2 | 8.36 | 900℃ | 925℃ |
Grades | Granule size | Scott density (g/c㎡) | Tap density (g/c㎡) | Hall flow (s/50g) | Binder (%) | |
Granules | MX4885-1 | 63 – 450 | 2.4 | 2.7 | 7 | 2.5 |
MX4381 | 63 – 450 | 2.4 | 2.7 | 6.5 | 2.5 |
NEXT®400, MX4885 and MX4380 powders are specially designed for the free sintering process. They combine both technological and economical advantages of the pre-alloyed solution.
Packing
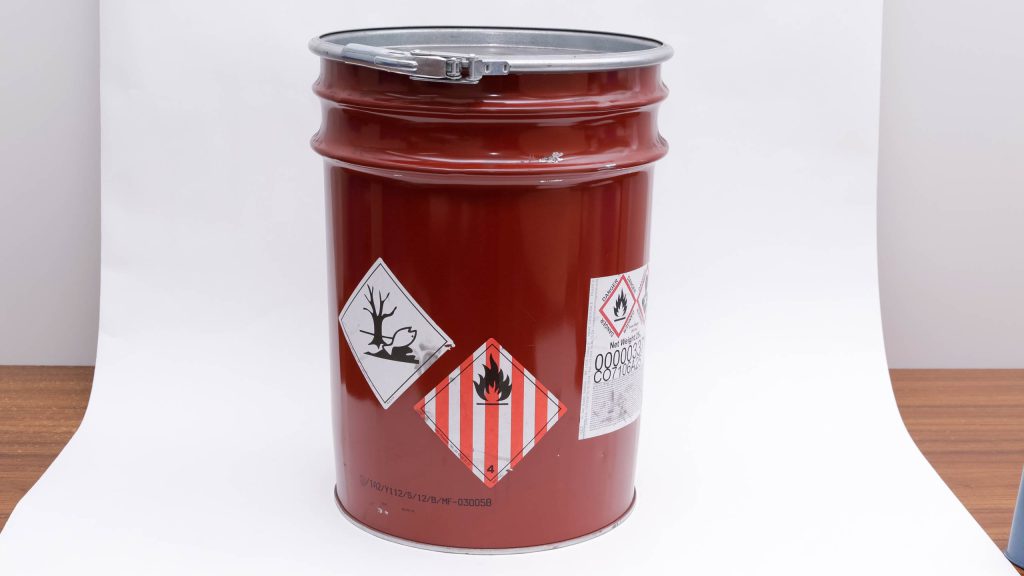
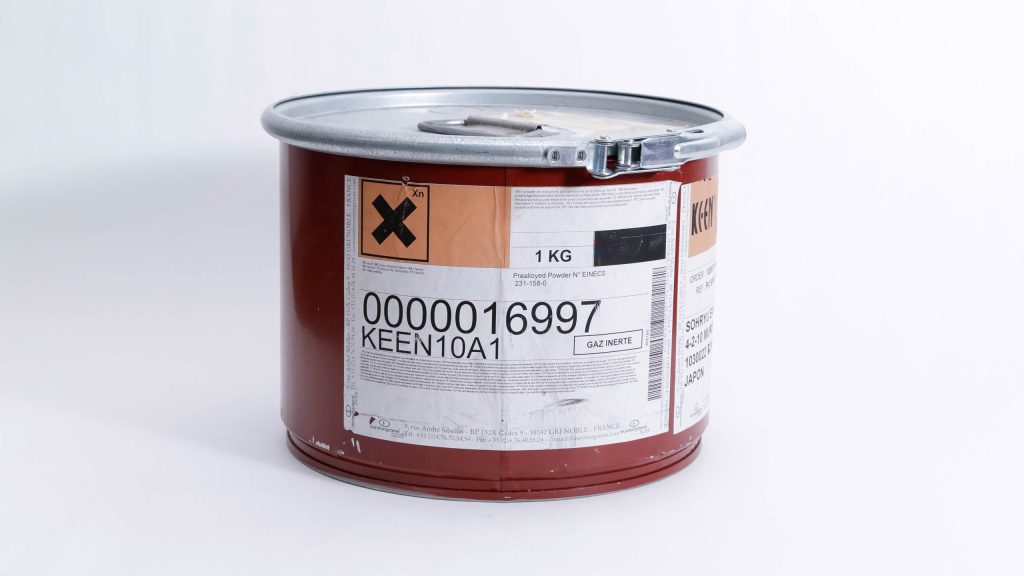